Ultrasonic welding has established a growing popularity in the automotive industry. It’s in large part due to the precision and reliability of ultrasonic joints, and undoubtedly due to its unmatched efficiency, both in cost and time. All these factors coincide favorably with the unique requirements and challenges of automobile manufacturers and their suppliers. It has widespread applications for various components and different stages of production.
The Mechanics of Ultrasonic Welding
The process of ultrasonic welding involves pressing two materials together under pressure while subjecting them to high-frequency vibrations. These vibrations generate frictional heat at the interface of the materials, causing localized melting. As the vibrations cease, the melted materials solidify, forming a durable bond.
Contrary to conventional welding techniques, ultrasonic offers some unique advantages. It allows us to join dissimilar materials, which can otherwise be quite challenging. It also reduces the risk of damaging or distorting the material like traditional welding methods that involve much higher heat and melting.
Benefits of Ultrasonic Welding in Automotive Manufacturing
Exceptional Strength and Durability
Components used for automobiles are often subjected to high degrees of stress and vibrations. They are also subject to strict safety regulations. Molecular bonds created with ultrasonic welding have exceptional strength and durability, therefore proving highly reliable.
High Precision and Consistency
The process of ultrasonic welding is precisely controlled and has minimal variations in joint quality. It produces highly consistent results, making it the perfect method for manufacturing critical components.
Improved Aesthetics
Ultrasonically welded joints are clean and have no visible seams. Lending its contribution to the visual appeal of the vehicle’s interior or exterior.
Automotive Components Utilizing Ultrasonic Joining Technology
Plastic Components Assembly
The inexhaustible abilities of joining plastics make ultrasonic technology essential for assembling parts such as dashboard panels and interior trim. It ensures secure joints without compromising the aesthetics of the vehicle’s interior.
Wiring Harnesses
With continuous development and increasing capability, ultrasonic remains the best available joining technology for wire splicing, which makes it invaluable to the automotive industry, especially in the pre-fabrication of wire harnesses. With the rough environmental conditions automobiles face throughout their service life, fault-free connections are crucial.
Battery Pack Encapsulation
In the rapidly developing segment of electric vehicles (EVs), ultrasonic welding is utilized for encapsulating battery packs. This ensures the integrity of the battery compartments, preventing moisture and contaminants from compromising the battery’s performance.
Battery Pack Busbars
Electric vehicle manufacturers are constantly demanding more powerful batteries in order to achieve greater ranges and faster charging. To reach high operating voltages and current, without taking too much space, an improved and compact conductor is required. It comes in the form of a flattened metallic bar, usually made from copper or aluminium, namely a busbar. Being able to fit inside battery bank enclosures and providing excellent conductive qualities as well as heat dissipation, it’s become a revolutionizing factor for battery pack manufacturers.
Ultrasonic welding ensures solid welds that preserve conductivity, while also saving production costs. It can weld dissimilar materials, such as aluminium or copper. This is particularly important in EV production, as aluminium is commonly used in battery systems due to its lightweight and high thermal conductivity, while copper is a preferred conductor for its superior electrical conductivity. Ultrasonic welding enables manufacturers to use both materials while maintaining a strong and reliable joint.
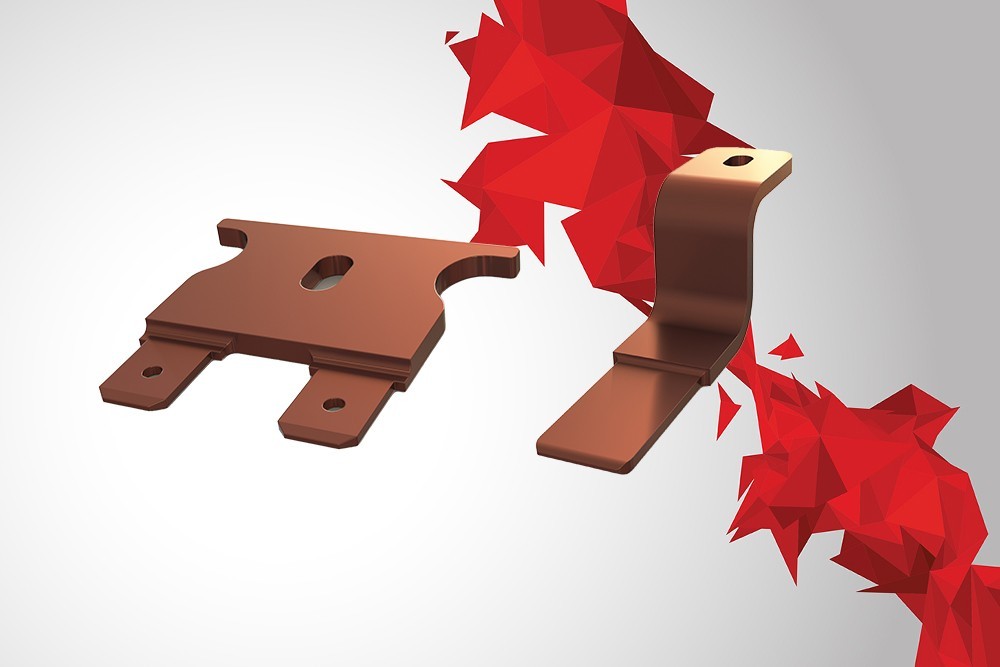
Advancements in Ultrasonic Welding
Real-time Monitoring and Quality Control
Modern ultrasonic welding systems incorporate real-time monitoring and quality control mechanisms. These features ensure that any deviations from the desired parameters are detected and can be corrected promptly, ensuring the highest standards of quality.
Environmental and Cost Efficiency
Ultrasonic welding stands out for its environmental friendliness and cost efficiency. With no need for consumables, such as additives or adhesives, it reduces waste and lowers costs, aligning with the industry’s sustainability goals.
Challenges and Limitations of Ultrasonic Welding
While ultrasonic welding offers numerous advantages, it’s not without its limitations. Joining materials with significantly different melting points can pose difficulties, therefore the process may not be suitable for all material combinations.
Conclusion
Ultrasonic welding has emerged as a game-changer in the automotive industry, offering a versatile and efficient solution for joining various materials. From enhancing the structural integrity of components to contributing to the aesthetics of vehicles, this technology plays a crucial role in modern automotive manufacturing. As the industry continues to evolve, ultrasonic welding is likely to remain a cornerstone of innovation, contributing to the development of safer, more durable, and environmentally conscious vehicles.
VIAL Automation is at the forefront of joining technology development and is pursuing high standards of quality and sustainability. That is why we are the ideal partner for your ultrasonic joining needs.
Reach out to our team to learn more about ultrasonic applications that might fit your company’s production needs.
We are here for you!
Ready to explore new opportunities? Contact us today to discuss your project requirements. Together, we can achieve precision, efficiency, and reliability in your manufacturing processes.
Follow us on social media: